Iron
Overview
Overview
Cast and wrought iron were popular building materials during the late 1700s and throughout the 1800s. Mass production meant that much Scottish architecture of this period used iron both decoratively and structurally. Scotland was also a major exporter of cast iron products in the 19th and 20th centuries.
Decorative and architectural ironwork was made using three ferrous metals: cast iron, wrought iron and mild steel, all of which came from ironstone. The characteristics of iron vary and while Scottish ores were well suited to casting, they were less suitable for converting into good wrought iron.
Regular inspection of ironwork will help you to spot any signs of damage or decay so that you can deal with them promptly. Iron is a durable material, but various factors can contribute to, and speed up, decay. Lack of regular maintenance and repairs is often the worst culprit.
Corrosion of iron occurs when oxygen and water are present. Over time, the iron returns to the natural oxide forms of the original iron ore it came from. Applying surface coatings to keep the iron dry reduces the risk of corrosion. You should remove any corrosion from ironwork as soon as you spot it.
Where repairs to iron are essential, intervention should be minimal and quality repair techniques should be used. Poorly designed repairs and replacements can cause severe damage and spoil the look and character of historic ironwork.
Replacement of iron elements may sometimes be necessary to ensure structural integrity. You must aim to keep as much of the original fabric as you can, however, and all replacements should be on a like-for-like basis.
Regular painting will keep ironwork looking good and help to protect it from corrosion. You may be able to make spot paint repairs if you’ve had to treat only small areas of corrosion.
Update your personalised ad preferences to view content
- Next
-
Characteristics
Characteristics
Characteristics
Decorative and architectural ironwork was made using three ferrous metals: cast iron, wrought iron and, less often, mild steel. The raw material for all three was ironstone. Its naturally occurring ores may feature other metal elements, giving the iron different metallurgical qualities.
Scottish ores were well suited to casting, but less suitable for conversion into good wrought iron. This is mostly to do with their high phosphorous content.
Scotland was never self-sufficient in structural wrought iron, and there are very few examples of fine decorative wrought ironwork across the country.
Cast iron
Cast iron is:
- very strong and hard
- highly durable
- able to be cast in intricate shapes
- more resistant to corrosion than wrought iron
Casting uses a pattern, usually made of wood, to make a mould out of special sand. Molten iron is poured into the mould and left to set into a rigid structure. The pattern can be reused to create designs with repeating identical sections.
Cast iron can’t be forged, and it is more brittle than wrought iron – it will shatter if struck by a sharp blow. This is due to its high carbon content (around 4%). Much of the carbon in ‘grey’ iron is in the form of graphite flakes, so a fresh break looks grey and crystalline.
Cast iron became a valuable structural material as soon as technological advances allowed it to be produced more cheaply and in large quantities.
Wrought iron
Wrought iron is iron in its almost pure form.
Wrought iron is:
- a ductile material
- highly workable
- fibrous in structure
- more resistant to corrosion than mild steel
Wrought ironwork tends to be quite ornate and delicate, as the material is so workable. Scrolls and foliage are common motifs, and patterns and designs typically vary slightly as wrought iron is worked by hand. Blacksmiths hammer the iron into shape, and then assemble it by fire welding and using collars, rivets and other mechanical means.
The term ‘wrought iron’ is often mistakenly used for any form of worked steel. But wrought iron is not the same material as mild steel.
- Previous
-
Overview
- Next
-
Inspection
Inspection
Inspection
Regular checks of ironwork will help you to spot any signs of damage or decay so that you can deal with them promptly.
Cast iron rainwater goods and iron railings and gates are among the most common forms of ironwork you’re likely to see in Scotland. Much structural ironwork is hidden from view.
Find out about the inspection of rainwater goods.
Learn about the inspection of iron railings and gates.
Properties that feature structural ironwork may sometimes need to have a structural appraisal.
Structural appraisal
You may seek a structural appraisal:
- for advice on the causes and structural significance of defects
- to correct structural problems you notice after a severe storm or fire
- before you buy or lease a property
- before repairing, refurbishing or converting a property
Site survey and inspection work provides information about a building’s physical condition. This is then used to assess whether the building can safely meet the needs of its users. Part of the structural appraisal will be to identify, and assess the structural significance of, past alterations.
A suitably qualified chartered civil or structural engineer should carry out, or at least supervise, the structural appraisal. The engineer may wish to consult a specialist in the conservation and repair of cast and wrought ironwork.
You may wish to entrust the inspection, conservation and repair of small iron structures to an experienced contractor.
- Previous
-
Characteristics
- Next
-
Corrosion
Corrosion
Corrosion
Iron corrodes, or rusts, when oxygen and water are present. Over time, the iron returns to the natural oxide forms of the original iron ore it came from. Applying surface coatings to keep the iron dry reduces the risk of corrosion.
Corrosion of iron may be sped up by:
- rainwater trapped and held in ‘water traps’
- various pollutants or salt in the air (e.g. by the sea)
- corrosive agents in materials next to the iron such as soil, masonry, mortar and concrete
- a galvanic reaction, caused by using unsuitable fixings or other metals, like mild steel, for repairs
Cast iron has far better natural resistance to corrosion than wrought iron, hence the long tradition of using cast iron for quality rainwater goods. But corrosion is a risk if the rainwater goods aren’t painted fully or often enough. Corrosion in hard-to-reach areas may not be spotted for some time.
Warning signs
Corrosion and general deterioration aren’t always visible, but a number of warning signs can point to problems in their early stages.
Warning signs include:
- ‘pitting’ on painted ironwork – this uneven surface is usually a sign that the iron is corroding beneath the paint (or has corroded previously)
- rust-coloured staining on supporting masonry – this has washed down from corroding ironwork
- oily residue on painted ironwork – tells you that the iron is corroding beneath the paint and/or that the oil based paint is breaking down
- blistering paintwork – a sign that corrosion is occurring under the paint
- plant growth – may signal the presence of water and dirt traps, which can speed up corrosion by stopping water from draining away
How to deal with corrosion
Remove any corrosion from ironwork as soon as you spot it. It’s important to protect masonry from staining and damage while you do this. You should then make good the paintwork to protect the iron against further corrosion.
You can remove corrosion using:
- a wire brush
- a chisel
- sandpaper
- another suitable mechanical means
Find out how to paint ironwork.
Progress of decay
Left untreated, corrosion will continue to eat away at the metal beneath the topmost layers of rust. As iron corrodes and delaminates (its layers separate) it ‘expands’, i.e. rust is greater in volume than the original iron.
Wrought iron will usually bend and distort as deterioration progresses, due to its malleability. Cast iron, a hard and brittle material, can break under the stress, often without warning. Corrosion is often to blame for cracked decorative cast iron elements.
- Previous
-
Inspection
- Next
-
Preventative maintenance
Preventative maintenance
Preventative maintenance
Iron is a durable material, but various factors can contribute to, and speed up, decay. Lack of regular maintenance and repairs is often the worst culprit.
Putting off basic maintenance tasks can lead to the need for costly repairs. For example, poorly functioning rainwater goods are often directly responsible for serious internal and external deterioration. Similarly, iron staining to masonry can be difficult to remove.
As iron tends to sit alongside timber, masonry, glass or other materials, a holistic approach to its conservation is needed. Neglecting one element of a building often causes other elements to fail.
You should pay special attention to basements and pavement light wells. Corrosion may be able to develop unseen in such environments – even to the point where structural integrity is affected.
Read about the maintenance of cast iron rainwater goods.
Find out about the maintenance of iron railings and gates.
- Previous
-
Corrosion
- Next
-
Repair techniques
Repair techniques
Repair techniques
Proper repair work is important. Poorly designed repairs and replacements can cause severe damage and spoil the look and character of historic ironwork, as well as not lasting very long.
Suitable materials must be used to make repairs. Traditional repair techniques should also be used, except where there’s firm scientific support for the use of a modern technique.
Examples of inappropriate repairs include:
- inserted sections made from other metals (e.g. aluminium or mild steel) – these will corrode at a faster rate when in direct contact with iron
- repairs carried out using poor quality welding (instead of traditional fire welding or mechanical fixings) can cause corrosion
- using the wrong pattern or shape
Mechanical repairs
Cracked castings often undergo mechanical repairs rather than hot repairs, as welding can subject cast iron to severe thermal stress and distortions.
‘Cold stitch’ repairs involve the blacksmith adding a wrought iron ‘stitch’ to repair the crack in a casting. A stitch repair can be made to appear almost invisible, but you should treat with caution any guarantee of structural performance. This technique is for decorative or for those under compression, only.
Before making repairs, the cause of the cracking must first be addressed to avoid the same problem arising in future.
Hot repairs
Cast iron can be difficult to fix and welding repairs don’t always last. Cast iron welding should only be carried out off site and by experienced craftspeople. Welding can damage cast ironwork if the wrong materials and methods are used. Fractures can sometimes be repaired using screws and dowels instead.
Welding high quality wrought iron, which has a low carbon and sulphur content, should present few problems.
Fillers
An epoxy-based metal filler can be used to make cosmetic repairs prior to painting. You shouldn’t use Ordinary Portland Cement or cement mortars as these are porous and will shrink more than the iron, allowing water to get in.
Using an inflexible filler (or cold stitching) may not be suitable for repairing castings that have cracks or wide gaps between joints. These may be the result of thermal or structural movements, which must first be rectified. Most iron structures need movement joints to be able to perform effectively.
Mechanical strengthening
Resin-bonded carbon fibre reinforcement is a modern, reversible technique. It has been used to reinforce the surface of concrete motorway bridges for some time and is now being used to strengthen historic iron bridges.
- Previous
-
Preventative maintenance
- Next
-
Replacement of elements
Replacement of elements
Replacement of elements
Iron elements may sometimes need to be replaced if they are missing or can't be repaired. You must aim to keep as much of the original fabric as you can, however, and all replacements should be on a like-for-like basis.
Any replacement made should also be proportionate to the damage. For example, there’s no need to replace an entire panel of cast iron railings to deal with a single damaged baluster.
Fixings should be selected with care. Galvanised fixings can rapidly corrode and shouldn’t be used. Stainless steel fixings are generally best.
Cast iron replacements
You can source matching cast iron parts from foundries specialising in traditional casting. Most hold a wide range of traditional patterns in stock. New castings moulded in green sand from well made wooden patterns can look as good as 18th and 19th-century originals.
Cast aluminium, steel, fibreglass and plastic are unsuitable substitutes and have a shorter lifespan. Money saved in the short term will be cancelled out by the need to renew inferior materials earlier than if using cast iron replacements.
Wrought iron replacements
Where decorative wrought iron has been lost, a replacement can be commissioned from a blacksmith. Wrought iron is no longer made and is only available as recycled material. While it can cost more than mild steel (the most commonly used alternative) wrought iron is also more durable. Using wrought iron for repair and replacement work is thus likely to prove more economical in the long run.
- Previous
-
Repair techniques
- Next
-
Painting
Painting
Painting
Regular painting will keep ironwork looking good and help to protect it from corrosion.
You may be able to make spot paint repairs for small areas of corrosion. The edges of existing paint should be feathered using sandpaper and the exposed metal painted over. New paint should overlap the existing paint.
Exterior ironwork shouldn’t be painted from November and February, when the damp and cold will prevent paint curing properly. You should also avoid painting in breezy conditions: wind-blown dust and dirt can reduce the effectiveness of new paint.
Painting preparation
To prepare existing paint that is sound:
- fill small holes with resin to prevent water seeping in and getting trapped
- reseal defective joints with linseed and red lead putty
- remove rust with a wire brush and sandpaper – never just paint over it
- clean the surface of dirt and grease
- roughen existing paint with sandpaper to help the new paint stick to it
- make sure the modern paint you plan to use is compatible with the original paint – check with the paint manufacturer if in doubt
Painting
For a complete repainting, use:
- a zinc-based primer as base coat
- micaceous iron oxide layer
- two coats of gloss paint
Brushes are usually the most effective means of applying paint to ironwork. Hard-to-reach areas such as the rear of rhones should be painted as far as possible.
Allow each coat to dry thoroughly before applying the next. This prevents the upper coats being damaged as solvents evaporate from the undercoats.
Paint thickness is important: several thin coats are more effective than fewer thick coats.
Some iron is supplied from the forge with a temporary coat of linseed oil and soot. Internal items can be left with this coating if desired.
Painting as protection against corrosion
Paint is less effective if:
- the iron surface hasn’t been properly cleaned and prepared before painting
- it has been applied too thickly
- the paint used is incompatible with iron
- too few coats of paint have been applied
- Previous
-
Replacement of elements
- Next
-
Permissions for work
Permissions for work
Permissions for work
You should check whether you must first apply for planning permission or any other type of consent before making any changes to historic ironwork of any kind. Listed building consent or conservation area consent may be needed, depending on the property and its location.
For listed properties, listed building consent may be required before repairs are made to original ironwork.
Contact your planning authority to find out more.
Find out more about listed building consent and conservation area consent.
Reinstatement of railings
You may need to get permission to reinstate railings and/or gates before work begins on site. You should check with your planning authority. Listed building consent will be required if your property is listed.
Painting ironwork of historic interest
If ironwork is listed or of special historical interest, the removal of original paint layers will need careful consideration and may merit the analysis of existing paint to work out the original colour scheme used.
- Previous
-
Painting
- Next
-
History
History
History
Cast and wrought iron were popular building materials during the late 1700s and throughout the 1800s. Mass production meant that much of the architecture of this period used iron both decoratively and structurally.
Retaining traditional ironwork can be hugely beneficial to the quality and character of a traditional building. Such period features add to the look and value of a property, and are costly to replace if removed.
As well as the cast iron rain goods, iron railings and gates and decorative ironwork that we can see around us, Scotland has much hidden ironwork. Cast iron in particular was a surprisingly popular choice for shop fronts and lintels, floor support and even entire façades.
Other architectural uses of iron included:
- structural columns, beams and girders
- roofing and ridge cresting
- railings, gates and finials
- balconies
- glasshouses
- bandstands
- pre-fabricated iron buildings
Iron production
Technological advances in the 1700s and 1800s enabled the mass production of wrought and cast iron, and iron production became a significant industry in Scotland. Before this time, large amounts of iron would have been used only for buildings of the highest status. Mass production made it much cheaper.
Cast iron began to be used extensively from the 1820s onwards, as Scotland developed into a global centre for such work. Major architectural iron founders were set up across the central belt, and most towns had a foundry that might make simple products. Iron was soon being used structurally, at first as framing for cotton mills like New Lanark, and later for all kinds of buildings.
Casting is the only way to shape cast iron. First a pattern is made, usually of wood. This is then used to make a mould using special sand. Molten iron is then poured into this mould and left to set. Wrought iron was manufactured from cast iron through the puddling process (heating and repeated hammering by hand).
Scotland’s cast iron manufacturers were world leaders in the production of cast iron items in the 19th century, and Glasgow alone had more than 800 foundries in operation. Illustrated catalogues featured large ranges of goods, and today it’s often possible to identify the original manufacturer by the marks they made on their products.
Wrought iron was used less widely in Scotland – though it enjoyed a revival in the early 1900s – and hasn’t been made since the 1960s. It is possible to source recycled wrought iron, however. The term ‘wrought iron’ is often mistakenly used to describe any kind of ornamental work in mild steel. ‘Wrought steel’ would be a more accurate description.
Scotland’s lost ironwork
Scotland’s streetscapes were significantly altered during the Second World War when large amounts of cast iron were collected to boost the malleable iron industry.
Much boundary ironwork was given up for the war effort, and often little survives other than railing stubs in boundary walls. Original examples of ironwork were sometimes left in streets for future reference or where removal may have caused a safety hazard.
- Previous
-
Permissions for work
- Next
-
Contacts
Contacts
Contacts
Get in touch if you have any questions. We will be happy to help.
- Technical Research Team
- 0131 668 8951
- technicalresearch@hes.scot
- Previous
-
History
- Next
-
Resources
Resources
Resources
Professional institutions
Publications
Inform guides
An introduction to conservation and maintenance of traditional buildings for complete beginners.
Care and Maintenance of Corrugated Iron
The Maintenance of Cast Iron Rainwater Goods
The Maintenance of Iron Gates and Railings
Short guides
Information on building conservation topics for home owners, trades people and building professionals.
4 – Maintenance and Repair Techniques for Traditional Cast Iron
Guides for practitioners
Information and advice for building professionals, developers, planners and conservation officers.
Technical Advice Notes
In-depth technical information for building conservation professionals.
20 – Corrosion in Masonry Clad Early 20th Century Steel Framed Buildings
29 – Corrugated Iron and other Ferrous Cladding
Historic Publications
Historic publications on building materials and techniques. These include historic trade catalogues for things like cast iron goods and prefabricated buildings.
Other resources
Building Scotland – Celebrating Scotland’s Traditional Building Materials
The Building Conservation Directory
- Previous
-
Contacts
Related to Iron
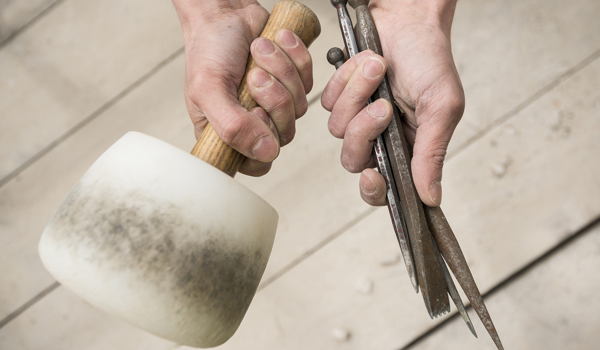
Hiring a contractor
Get advice on hiring a contractor including choosing a contractor and managing the work.