- Home
- Building Advice
- Building components
- Roofs
- Roofing leadwork
Roofing leadwork
Overview
Overview
Lead is a soft, malleable and extremely resilient heavy metal, making it ideal for widespread external use in construction.
Roofing leadwork is used mainly to stop rainwater from entering junctions between roof elements and to channel water off a building. It also has decorative uses.
Lead expands and contracts as weather conditions change, and detailing must allow for this to prevent stresses forming in the lead sheet.
Regular inspections of roofing leadwork can reveal defects before they cause problems. Additional checks should be made after storms or gales: strong winds may distort leadwork or lift it from its original position, letting in water.
Other common causes of problems with roofing leadwork include chemical damage, concentrated water flow, and improper installation – all of which can lead to corrosion.
Evidence shows that lead can perform satisfactorily for more than 100 years. With proper maintenance and repairs, your roofing leadwork can effectively and reliably help to keep your roof weatherproof and watertight.
Update your personalised ad preferences to view content
- Next
-
Characteristics
Characteristics
Characteristics
Lead is a soft, malleable and extremely resilient heavy metal, making it ideal for widespread external use in construction. Lead sheet comes in different thicknesses and weights (codes) for different functions.
Roofing leadwork is used mainly to:
- stop rainwater from entering complex junctions that would otherwise be very difficult to keep weatherproof
- channel rainwater off a building and dispose of it elsewhere
Lead is one of the most durable metals used in building. Evidence shows that it can perform satisfactorily for more than 100 years. The thicker the lead sheet, the more durable it will be.
Detailing must allow for the lead to expand and contract as weather conditions change.
Freshly cut lead has a bluish white colour, but patination oil is normally applied. Exposure to the air causes a reaction that turns the lead a dull grey and produces in it a natural resistance to corrosion.
Applications and uses
Roofing leadwork is likely to be found on many traditional buildings in Scotland.
Leadwork may be used for:
- access hatch covers and roof lights
- flashings – whether apron, chimney, cover, dormer or gable
- bay windows
- flat roofs
- parapet gutter lining and parapet wall capping
- rainwater downpipes and outlets
- roof ridges and roof hips
- valley gutters and secret gutters
- vertical cladding
- weatherproofing cornices
Lead can be used decoratively as well as for this very wide range of functions. Its malleable qualities mean that it can be easily worked into architectural features such as scalloped detailing, raised bosses and ball finial decorations.
- Previous
-
Overview
- Next
-
Inspection
Inspection
Inspection
Roofing leadwork should be checked regularly including at least once in the autumn, before winter weather sets in. This gives you the best chance of spotting – and correcting – defects before they cause problems.
Strong winds may distort leadwork or lift it from its original position, particularly if fixings are inappropriate, loose or inadequate. So you should also make extra checks after any storms or gales.
Initial inspection
Check the roof from outside, standing at ground level. Follow the line of individual roofing leadwork items to check if any areas are bent or out of place. Using binoculars will help you to see the roofing leadwork more clearly.
You should also check the internal roof space for signs of leaks, for example, staining of the roofing joinery. Such signs may not be obvious from the outside but may point to external problems with the roofing leadwork.
Note down any concerns or signs of problems to discuss with the contractor who will carry out the repair work.
Roof-level inspection
Roofing leadwork should be closely inspected for any areas of deterioration or damage.
Your contractor should look for signs of:
- movement
- distortion
- corrosion
- puncture damage
- staining or small holes – especially in areas of concentrated water flow
- cuts, rips, tears or cracking
- surface ripples and buckling – such stresses may signal restricted thermal movement
- lichen, moss and algae surface growths
- missing or loose clips and other fixings
Parapet gutters and other water outlets should also be checked for blockages, particularly in autumn.
- Previous
-
Characteristics
- Next
-
Common causes of problems
Common causes of problems
Common causes of problems
Roofing leadwork is at risk from chemical damage, wind lift, concentrated water flow, lead theft and improper installation.
Chemical damage
Lead resists corrosion well, but it can be damaged or stained by:
- alkalis from new cement
- acids from some timbers (oak in particular)
- the run-off from lichen, moss and algae surface growths
Temporary protection may be called for when working with cement or lime mortars near to lead. An appropriate barrier (e.g. a suitable underlay) may be necessary between lead and timber. Biological growths shouldn’t be allowed to get established near lead or to build up on its surface. Patination oil gives a degree of protection.
Wind lift and distortion
Wind can lift and distort lead flashings not held securely in place. The number of clips needed to do so will depend on the size and function of the item of leadwork and how exposed its position on the building. Copper, stainless steel or lead clips should be used to avoid harmful reactions.
Roof ridges and roof hips, often made of lead, can be dislodged if the fastening or bedding fails. Thermal action can gradually lift the nails from ridges and hips and eventually such elements can be blown off.
Concentrated water flow
Lead lined parapet gutters can fail due to wear and cracking of the lead, blockages or metal theft. Large amounts of water can enter the building fabric through the wall head as a result, causing serious and progressive damage to the sarking (wooden boards). Structural damage will follow if the failure isn’t corrected.
Lead valleys can be worn through by:
- the action of water
- puncture damage from falling objects
- cracking
Staining can signal areas of concentrated water flow and possible failure. Over time, staining may develop into small holes, which will let in enough water to cause timber decay to progress.
Valleys and junctions have a finite life, although suitably specified lead generally lasts much longer than zinc. A temporary repair using a suitable sealing tape or material may be appropriate.
Improper installation
Other physical defects include:
- surface ripples and creep
- rips and tears
- restricted thermal movement
- topside and underside corrosion
Some of these issues can be avoided by laying the lead sheet correctly in the first place. Large sheets of lead should be supported on smooth roof decking, with a suitable underlay placed between the lead and deck.
Underlay should:
- act as sound deafening
- allow for thermal movement
- not contain any material detrimental to lead
- provide a barrier against corrosion – e.g. from contact with timber
- provide an even support surface
- reduce the risk of trapped moisture and condensation below the lead sheet
Laying the wrong material in this position could ‘glue’ the layers together in hot weather, causing the lead sheet to buckle and fracture. Bituminous roofing felt must be avoided for this reason. An appropriate building paper or polyester geotextile material is preferred.
- Previous
-
Inspection
- Next
-
Maintenance and repairs
Maintenance and repairs
Maintenance and repairs
Knowledge and experience is needed to correctly assess and diagnose the cause of roofing leadwork defects before carrying out any repair work.
A suitable contractor will consider:
- the overall condition of the lead
- how long it's been in place
- whether there are any inherent design faults
- whether there's any interaction between the lead and other materials or growths nearby
Patch repairs
Small cuts, rips and tears in lead parapet gutters can be temporarily repaired by applying bituminous backed foil. But a more appropriate repair might be carried out by carefully welding small patches of lead over the damaged area.
Extreme care must be taken when any hot work is carried out to avoid the risk of fire. It may be safer to carry out patch repairs off site, by carefully removing the damaged piece of lead from the roof for welding.
Parapet gutters should also be fitted with an overflow outlet. That way, if the rainwater outlet becomes blocked, pooled water can escape without flooding into the building interior.
Roofing leadwork that eventually fails can be stripped off and sold for scrap – it can then be recycled and circulated for reuse as new sheet.
Fixings and fastenings
The free edge of all lead flashing should be clipped in place to prevent lifting and distortion by the wind. Clips are usually made of copper, stainless steel or lead, to avoid harmful reactions. How many clips are used will depend on the size and function of the item of leadwork and how exposed its position on the building.
Roof ridges and roof hips, often made of lead, can be dislodged if the fastening or bedding fails.
Lead can expand and contract significantly as the weather changes. If roofing leadwork is fixed too firmly in place, stresses will result from this thermal movement. These can then lead to failure of the lead through distortion, buckling and cracking.
Detailed guidance on the optimum sizes of lead to use for different purposes is available to the construction industry. This should be followed when repair works are carried out to help ensure that the lead performs correctly afterwards.
The guidance may suggest changing the original detailing of the building to ensure that sufficient ‘falls’ and ‘steps’ are in place – as well as using the correct size of sheet – when lining parapet gutters or covering a flat roof. The fall is the incline of the lead roof: usually not very steep but enough of a drop to ensure that water runs off and doesn't pool. Steps are the little ridges over joints between lead sheets that allow for thermal expansion and contraction. The size of lead sheet that can be used without adding such steps is limited.
As lead reacts badly to some metals:
- copper or stainless steel nails should be used to secure sheets in place
- fixing screws should be brass or stainless steel
Fixings made through the sheet should be covered with lead ‘dots’ to stop water getting in.
Choosing a contractor
In the right hands, lead is effective, reliable and indispensable in the care of traditional buildings. But its correct use does depend on the craftsperson using it having suitable training and experience in the art of lead working.
You should seek appropriate advice if repair or replacement works are likely. Exercise caution if replacement materials such as fibreglass or vinyl are offered in the course of leadwork repairs.
Find out more about hiring a contractor.
- Previous
-
Common causes of problems
- Next
-
Permissions for work
Permissions for work
Permissions for work
You should check whether you must first apply for planning permission or any other type of consent before making any changes to roofing leadwork. Listed building consent or conservation area consent may be needed, depending on the property and its location. Contact your planning authority to find out more.
Learn more about listed building and conservation area consent.
- Previous
-
Maintenance and repairs
- Next
-
History
History
History
Lead’s long history of use goes back to Roman times. It is one of the most durable metals used in construction. Evidence shows that it can perform satisfactorily for more than 100 years.
Sheet lead production
Sheet lead can be made in one of three ways:
- milling (rolled)
- sand casting
- machine casting
Milling
For most purposes, rolled sheet (milled sheet) is the form of lead usually used today. The rolling technique was first used to make sheet lead around the mid-1700s.
A block of lead is rolled between cylindrical rollers to make milled lead sheet. The rollers are gradually brought closer together until the sheet is the required thickness. Rolled milled sheet has a smooth finish on both sides and is the same thickness all over.
Sand casting
The Romans made sand cast sheets of lead to create water storage tanks and pipes. In medieval times, many church and cathedral roofs were covered with lead made in a similar manner.
Some specialist firms still carry out the process of sand casting.
Molten lead is poured across a bed of sand and spread out by hand to the required thickness. The lead solidifies to form a sheet with a distinctly rough surface on the underside.
Machine casting
Machine casting was invented in the 1950s and introduced in Scotland in the 1980s.
A cool metal drum is rotated in a bath of molten lead, and the liquid metal then solidifies on the cooled surface of the drum. This is then peeled off as a single, smooth sheet of lead.
Sheet thickness can be varied by altering the:
- rotation speed of the drum
- depth to which the drum is immersed in the molten lead
- temperature difference between the drum and molten lead
- Previous
-
Permissions for work
- Next
-
Contacts
Contacts
Contacts
Get in touch if you have any questions. We will be happy to help.
- Technical Research Team
- 0131 668 8951
- technicalresearch@hes.scot
- Previous
-
History
- Next
-
Resources
Resources
Resources
Professional institutions
Lead Sheet Association
Lead Contractors Association
The National Federation of Roofing Contractors
Confederation of Roofing Contractors
The Institute of Roofing
Publications
Inform guides
An introduction to conservation and maintenance of traditional buildings for complete beginners.
Short guides
Information on building conservation topics for home owners, trades people and building professionals.
2 - Lead Theft : Guidance on Protecting Traditional Buildings
Other resources
- Previous
-
Contacts
Related to Roofing leadwork
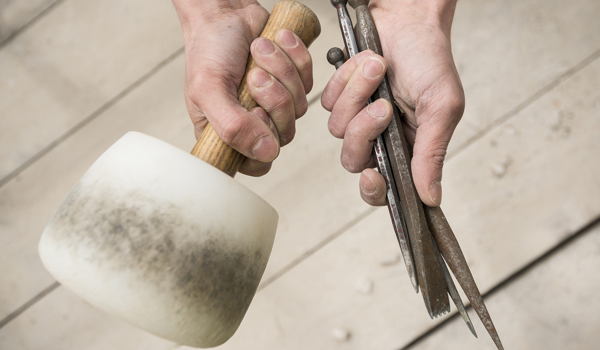
Hiring a contractor
Get advice on hiring a contractor including choosing a contractor and managing the work.