- Home
- Building Advice
- Building components
- Roofs
- Corrugated iron roofs
Corrugated iron roofs
Overview
Overview
Corrugated iron is relatively light, portable and adaptable, which made it ideal for some traditional construction. It was most frequently used for roofing and walling, and also for prefabricated buildings, especially in rural areas.
All metals corrode. So the main aim with a corrugated iron roof is to slow down how quickly this happens. Regular inspections can help you to spot and fix problems before they become serious.
Wetting and drying cycles speed up the decay of a corrugated iron roof. Trapped moisture caused by vegetation and clogged rainwater goods are common causes of problems with corrugated iron roofs, as is condensation build-up inside.
Reuse of original corrugated iron sheets is preferred over replacement, as the few firms making sheets today may be unable to match profiles and sizes. Patch repairs of existing sheets are possible.
Corrugated iron roofs are very much part of Scotland’s rural landscape. Traditional materials and colours should be used for over-painting sheets, preferably to match those originally used.
- Next
-
Characteristics
Characteristics
Characteristics
Corrugated iron is relatively light, portable and adaptable, which made it ideal for traditional construction. Made by passing thin flat iron sheets through rollers, the corrugations provided rigidity and added structural strength.
A broad range of ironworkers made corrugated iron sheets up until the 1920s. The sheets came in various lengths, usually up to a maximum of 10 feet. Gauges (thicknesses) ranged from around 0.5mm to 1.5mm depending on the end use. Corrugated iron is still made today, though it comes in a limited range of gauges.
Sheet pitch and profiles
Pitch is used to describe the distance between the topmost points of two peaks in a sheet of corrugated iron.
A wide variety of pitches were available, and standard dimensions ranged from 25mm to 153mm. For domestic purposes, a 76mm pitch was common.
Corrugated iron sheets also came in a range of profiles, for example:
- regular curved peaks and troughs – sometimes known as 'sinusoidal'
- curved corrugations with an area of flat edging
- ‘weatherboard’ or stepped corrugations (rather than curved)
- small, wide-spaced ribbed corrugations
The sheet corrugations lent themselves well to lap joints, often overlapping by 150mm and by one or two corrugations where sheets are next to one another.
Protective coatings
Various coatings were used to protect corrugated iron from the weather, although coating failure is common. Popular options were oil based paints (usually linseed) and red lead paint. Pitch and bitumen were also used to a lesser extent.
Galvanising the iron with zinc, to protect it from rust, was increasingly common by the late 1800s. Galvanising involved dipping the iron sheet into a bath of molten zinc to form a protective layer over its surface.
A number of patented ‘rustless coatings’ were developed in the late 1800s and early 1900s. Often known as the ‘Barff process’, after the inventor, these coatings formed protective oxide layers on the surface of the metal.
Perforated sheets were also developed, to tackle the problem of condensation.
Construction
Corrugated iron was used frequently for roofing and walling, and less often for fencing and other innovative uses.
Manufacturers soon developed other components so that a building could be constructed from a frame and corrugated sheet. Ridging details, ventilators, windows and most other such components can no longer be sourced.
Specialist fixings were needed for the corrugated sheets, particularly given the various profiles available. Original hooks and bolts (which were usually galvanised) and specially shaped washers (to make watertight seals) should be cleaned and reused.
Prefabricated structures could be erected by securing corrugated sheets to an internal timber or metal frame. This was sufficient for agricultural purposes, or such structures could be internally insulated and covered in timber lining or plaster to meet domestic needs. Many prefabricated buildings such as chapels, mission halls, hospitals and trading posts were manufactured in Britain for use across the country and for export purposes.
- Previous
-
Overview
- Next
-
Inspection
Inspection
Inspection
Corrosion (rust) is the main cause of concern with a corrugated iron roof. Regular inspections followed by maintenance and repairs may help you to slow down the rate of decay.
Always check your roof at least once in the autumn, before the winter weather sets in. And be sure to carry out extra checks after any storms or gales.
Look out for:
- coating failure
- damage caused by moss or other vegetation trapping moisture against the sheets
- clogged rainwater goods or corrugations affecting drainage
- rainwater run-off from a rusted roof seriously (and permanently) staining masonry walls below
- leaks caused by corrosion in the sheets
- failed seals at junctions between sheets and components
- condensation build-up on the interior or underside of sheets
Initial inspection
You should check a corrugated iron roof from inside as well as from outside at ground level. Note down any concerns or signs of problems to discuss with the contractor who will carry out the repair work.
Roof-level inspection
The roof surface should be checked for signs of corrosion and poor drainage of rainwater. Avoid walking directly on the roof.
Gutters and other water outlets should be checked for blockages, particularly in autumn.
- Previous
-
Characteristics
- Next
-
Common causes of problems
Common causes of problems
Common causes of problems
Corrugated iron roofs (and buildings) are particularly susceptible to corrosion, which can lead coating loss, loss of structural strength or loss of entire sheets.
Corrosion
All metals corrode. So the main aim when dealing with a corrugated iron roof is to slow down how quickly this happens.
Corrugated iron sheets are impermeable to moisture. But while rain is kept out, condensation is trapped in. Wetting and drying cycles are the main cause of decay, both inside and out.
Corrosion occurs faster where:
- moss or other vegetation traps moisture against the sheets
- rainwater doesn’t run off the roof effectively
- condensation is trapped against the roof’s interior
Corrosion can lead to:
- coating loss
- loss of structural strength or integrity
- the complete loss of the sheets
Coating failure
Coating failure is common on galvanised surfaces. Effective coating requires the use of either a mordant wash to provide a chemical etch for the primer layer, or an etching primer for galvanised surfaces. Often, neither was used.
The oxidised surface (rusted appearance) that results from coating failure is often thought attractive due to its natural colouration. In many cases, the rusted roofs are seen as an integral part of the rural landscape.
Rainwater run-off from a rusted corrugated iron roof can cause serious staining to masonry below, however. This is virtually impossible to remove from exposed stone.
- Previous
-
Inspection
- Next
-
Maintenance and repairs
Maintenance and repairs
Maintenance and repairs
Corrosion affects all metals, but regular maintenance and repairs will help to slow its progress and keep your roof watertight.
Repairs should focus on the minimum work necessary, as this reduces the risk of losing historic material. Where dismantling is required to make full repairs, undue stress mustn’t be placed on other components.
General maintenance
Regular roof maintenance tasks include:
- removing any moss or other vegetation close to sheets
- cleaning gutters and general upkeep of rainwater goods
- replacing failed seals at junctions between sheets and components
Reuse vs replacement
You should always aim to retain the original sheets. Some firms still make corrugated iron, but matching profiles and sizes may be no longer available.
Patch repairs of existing sheets are technically possible. But the thin gauge of metal makes such repairs difficult to achieve.
New sheets shouldn’t be fitted directly on top of existing corroding sheets. This will trap moisture, and speed up rusting of the new sheet by creating a ‘corrosion cell’. Capillary action between the sheets is also likely to cause moisture to move and get trapped.
Painting
You should try to match the original paint colour if over-painting corrugated iron sheets. This may be visible on existing ironwork, or other local examples might give you an idea of what the original colour was likely to have been.
Red lead paint was widely used for corrugated iron roofs (and walls) and is still available to buy. You don’t need consent to use red lead paint as it contains no harmful lead compounds. Green and red colours were fairly common too, as were creams and browns in the 1900s.
Choosing a contractor
It’s best to employ a firm experienced in the repair of traditional ironwork. But be aware that few firms will have worked with corrugated iron.
You could also consider using a sheet metal worker who appreciates the historic qualities of corrugated iron and knows how it performs.
Find out more about hiring a contractor.
- Previous
-
Common causes of problems
- Next
-
Permissions for work
Permissions for work
Permissions for work
You should check whether you must first apply for planning permission or any other type of consent before making any changes to a corrugated iron roof. Listed building consent or conservation area consent may be needed, depending on the property and its location. Contact your planning authority to find out more.
Learn more about listed building and conservation area consent.
- Previous
-
Maintenance and repairs
- Next
-
History
History
History
Corrugated iron was patented in 1828 and used extensively in traditional construction. But today it is much undervalued as a building material.
Relatively light, portable and adaptable, corrugated iron was often used to replace or cover a thatch roof, or to construct large agricultural and industrial buildings.
Corrugated iron production
Scotland’s architectural iron industry was world leading at the end of the 1800s. Scottish firms such as Robertson and Lister, A J Main, and William Bain and Co. came to specialise in the manufacture of iron building components and entire buildings made of corrugated iron.
Thin flat iron sheets were passed through rollers to create the corrugations, providing rigidity and added structural strength. Galvanising the iron with zinc, to protect it from rust, was more and more common by the late 1800s.
A broad range of ironworkers made corrugated iron sheets up until the 1920s. The sheets came in various lengths, usually up to a maximum of 10 feet. Thicknesses ranged from around 0.5mm to 1.5mm depending on the end use.
Preserving historic material
A manufacturer’s nameplate may be visible on entirely prefabricated buildings. You could use this to search Canmore and other archives for more information about the property.
Corrugated iron roofs have saved many vernacular buildings. Beneath the sheets may be a relatively intact thatched roof – kept as insulation – or a traditional cruck frame. Both are worthy of preservation.
- Previous
-
Permissions for work
- Next
-
Contacts
Contacts
Contacts
Get in touch if you have any questions. We will be happy to help.
- Technical Research Team
- 0131 668 8951
- technicalresearch@hes.scot
- Previous
-
History
- Next
-
Resources
Resources
Resources
Professional institutions
The National Federation of Roofing Contractors
Confederation of Roofing Contractors
The Institute of Roofing
Publications
Inform guides
An introduction to conservation and maintenance of traditional buildings for complete beginners.
Care and Maintenance of Corrugated Iron
Technical Advice Notes
In-depth technical information for building conservation professionals.
29 – Corrugated Iron and Other Ferrous Metal Cladding
Other resources
- Previous
-
Contacts
Related to Corrugated iron roofs
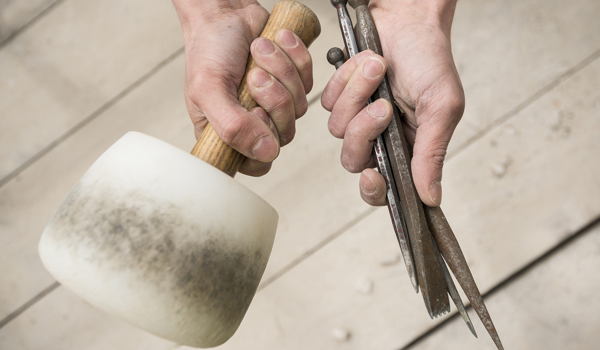
Hiring a contractor
Get advice on hiring a contractor including choosing a contractor and managing the work.