- Home
- Building Advice
- Building components
- Iron railings and gates
Iron railings and gates
Overview
Overview
Retaining traditional ironwork such as gates and railings can be hugely beneficial to the quality and character of a traditional building. Such period features add to the look and value of a property, and are costly to replace if removed.
Many buildings in Scotland have lost their original boundary ironwork (railings and gates) through damage or deterioration, or in support of the war effort during the Second World War.
To work out how best to maintain or repair ironwork, you first need to know what type of iron you’re dealing with. Cast ironwork is generally flatter in appearance and heavier in design than wrought ironwork and is more often found in Scotland. Wrought ironwork, which is less common, tends to be quite ornate and delicate, as wrought iron is highly workable.
Regular inspections will help you to spot any signs of damage or decay so that you can deal with them promptly. Trapped water, lack of protection, fractures and impact damage and the progress of decay are common causes of problems with iron railings and gates.
Quality maintenance and repair work is vital. Poorly designed repairs and replacements can cause severe damage and spoil the look and character of historic ironwork. Replacements should always be on a like-for-like basis, and you should aim to replace only those sections of ironwork that are missing or beyond repair.
Boundary ironwork was traditionally painted a single colour and periodic painting – to match the original scheme – will protect ironwork and keep it looking good.
You may require permissions for work including repairs and the reinstatement of railings and gates, particularly if your property is a listed building.
- Next
-
Characteristics
Characteristics
Characteristics
To work out how best to maintain or repair ironwork, you first need to know which of the two types of iron you’re dealing with.
Cast iron
Cast ironwork is more often found in Scotland than wrought ironwork. It is generally flatter in appearance and heavier in design than wrought ironwork.
First a pattern is made, usually of wood. This is then used to make a mould using special sand. Molten iron is then poured into this mould and left to set into a rigid structure.
Because the pattern can be reused, designs often tend to have repeating identical sections.
Wrought iron
Although wrought ironwork is less common in Scotland, it enjoyed a revival in the early 1900s.
Wrought ironwork tends to be quite ornate and delicate, as wrought iron is a wonderfully workable material. Scrolls and foliage are common motifs, and patterns and designs typically vary slightly as it’s worked by hand. Blacksmiths hammer the iron into shape, and then assemble it by fire welding and using collars, rivets and other mechanical means.
The term ‘wrought iron’ is often mistakenly used for any form of worked steel. But wrought iron is not the same material as mild steel.
- Previous
-
Overview
- Next
-
Inspection
Inspection
Inspection
Regular checks will help you to spot any signs of damage or decay so that you can deal with them promptly.
Annual inspections should check for:
- damage to paint coatings
- signs of corrosion
- plant growth
- missing sections
- damage to cope stones
Remove any corrosion from the ironwork as soon as you spot it. It’s important to protect masonry from staining and damage while you do this.
You can remove corrosion using:
- a wire brush
- a chisel
- sandpaper
- another suitable mechanical means
Signs of deterioration
Corrosion and general deterioration aren’t always visible, but a number of warning signs can point to problems in their early stages.
Warning signs include:
- ‘pitting’ on painted ironwork – this uneven surface is usually a sign that the iron is corroding beneath the paint (or has corroded previously)
- rust-coloured staining on supporting masonry – this has washed down from corroding ironwork
- oily residue on painted ironwork – tells you that the iron is corroding beneath the paint and/or that the oil based paint is breaking down
- blistering paintwork – a sign that corrosion is occurring beneath the paint
- plant growth – may signal the presence of water and dirt traps, which can speed up corrosion by stopping water from draining away
- Previous
-
Characteristics
- Next
-
Common causes of problems
Common causes of problems
Common causes of problems
Iron is a durable material, but a number of factors can contribute to, and speed up, decay. Lack of regular maintenance and repairs is often the worst culprit.
Trapped water
Corrosion tends to occur more often at water traps. Rainwater is trapped and held in these areas, preventing ironwork from drying out and leaving it more prone to corrosion.
Water traps may be caused by:
- design flaws in the ironwork
- unsealed joints and holes
- a build-up of dirt
- damaged or flaking paint
- areas of previous corrosion
- plant growth
Where plants grow near to ironwork, roots and tendrils can damage ironwork as they grow. Developing corrosion may also be hidden from view.
Lack of protection
Paint is less effective if:
- the iron surface hasn’t been properly cleaned and prepared before painting
- it has been applied too thickly
- the paint used is incompatible with iron
- too few coats of paint have been applied
Fractures and impact damage
Unstable or subsiding supporting masonry can cause cast iron to fracture.
Impact damage may occur at vulnerable areas. Wrought ironwork can be severely distorted by an impact, while cast iron is likely to shatter.
Progress of decay
As iron corrodes and delaminates (its layers separate) it ‘expands’, i.e. rust is greater in volume than the original iron.
As deterioration progresses, wrought iron will usually bend and distort due to its malleability. Cast iron, a hard and brittle material, can break under the stress, often without warning.
The ironwork design may distort as its various elements are forced apart. Fracturing can occur to stone if ironwork fixed to masonry sockets corrodes and expands.
- Previous
-
Inspection
- Next
-
Maintenance and repairs
Maintenance and repairs
Maintenance and repairs
Regular maintenance and repairs will help to ensure that your ironwork has a long life.
Quality repair work is vital. Poorly designed repairs and replacements can cause severe damage and spoil the look and character of historic ironwork.
Examples of inappropriate repairs include:
- inserted sections made from other metals (e.g. aluminium or mild steel) – these will corrode at a faster rate when in direct contact with iron
- repairs carried out using poor quality welding (instead of traditional fire welding or mechanical fixings) can cause corrosion
Survey existing ironwork
The condition of existing ironwork should be assessed before repairs are made to decide how much work, if any, is required. Generally it’s best to intervene as little as possible.
Where repairs are necessary:
- keep as much of the original fabric as you can
- ensure that suitable materials and methods are used
Cast iron repairs
Cast iron can be difficult to fix and welding repairs don’t always last. Cast iron welding should only be carried out off site and by experienced craftspeople. Welding can damage cast ironwork if the wrong materials and methods are used. Fractures can sometimes be repaired using screws and dowels instead.
Replacements should always be on a like-for-like basis, and you should aim to replace only those sections of ironwork that are missing or beyond repair. You can source items from foundries specialising in traditional casting, which usually hold a wide range of traditional patterns in stock. So matching parts may be easier than you think.
Cast aluminium, steel, fibreglass and plastic are unsuitable substitutes and have a shorter lifespan. Money saved in the short term will be cancelled out by the need to renew inferior materials earlier than if using cast iron replacements.
Fixings should be selected with care. Galvanised fixings can rapidly corrode and shouldn’t be used. Stainless steel fixings are generally best to use.
Wrought iron repairs
A suitable qualified and experienced professional should carry out any essential repairs to wrought ironwork. Traditional detailing and techniques must also be used.
Wrought iron is no longer made and is only available as recycled material. While it can cost more than mild steel (the most commonly used alternative) wrought iron is also more durable. Using wrought iron for repair and replacement work is thus likely to prove more economical in the long run.
Find out about hiring a contractor.
- Previous
-
Common causes of problems
- Next
-
Painting
Painting
Painting
Boundary ironwork was traditionally painted a single colour and should be periodically repainted to match. New ironwork should be painted before reinstatement. The use of gold paint on railing heads was unusual and so should be avoided today.
Spot paint repairs may work for smaller corroded areas. The edges of existing paint should be feathered using sandpaper and the exposed metal painted over. New paint should overlap the existing paint.
Ironwork shouldn’t be painted from November to February, when the damp and cold will prevent paint curing properly. You should also avoid painting in breezy conditions: wind-blown dust and dirt can reduce the effectiveness of new paint.
Painting preparation
To prepare existing paint that is sound:
- remove rust with a wire brush and sandpaper – never just paint over it
- fill small holes to prevent water seeping in and getting trapped
- reseal defective joints with an oil putty
- clean the surface of dirt and grease
- roughen existing paint with sandpaper to help the new paint stick to it
- make sure the modern paint you plan to use is compatible with the original paint – check with the paint manufacturer if in doubt
Painting method
For a complete repainting, use:
- two coats of a zinc-based primer
- one coat of micaceous iron oxide
- two coats of gloss paint
Brushes are usually the most effective means of applying paint to ironwork.
Allow each coat to dry thoroughly before applying the next. This prevents the upper coats being damaged as solvents evaporate from the undercoats.
Paint thickness is important: several thin coats are more effective than fewer thick coats.
- Previous
-
Maintenance and repairs
- Next
-
Reinstatement
Reinstatement
Reinstatement
A small number of iron founders continue to specialise in architectural cast ironwork. Many hold patterns in stock, which may match your needs, or you can pay for a new pattern to be made in timber. It may be helpful to share the cost of such work with neighbours who have similar needs.
Wrought iron is no longer made, although recycled material can be sourced.
Removal of existing railings
Removing original railing stubs from boundary walls can be straightforward (or may already have been done as part of the war effort) leaving a socket that can be reused. Removing both the stub and its lead surroundings may be more difficult, although not impossible.
Stubs can be left in place and new ironwork installed between the original fixings, provided the original design allows for this. Each individual casting should be secured into the masonry as originally fixed. Inserting a lower bar horizontal to the wall is not recommended.
Casting new railings
Castings were traditionally made in grey iron to a specific mix that produced sharp detail.
Some firms promote the use of spheroidal graphite instead, as this is more resistant to impact damage. You must check, however, that the firm can deliver the required quality and detail of surface finish using this material.
Castings should:
- be clean and sharp
- have no jointing mismatch where the two moulds have come together
- be free of blowholes and other imperfections
You may wish to ask for an initial sample to approve before any further castings are made.
Fitting new railings
Ironwork should be secured into the clean and dry boundary wall sockets using hot poured lead, which is then tamped down when cool. A reputable contractor will be aware of the health and safety issues around the use of hot lead.
Using lead is a reversible approach, and it will contract and expand at roughly the same rate as the iron. It also offers a degree of corrosion resistance to the iron. The lead should be finished around the fixing to shed water away from the railing root and onto the stone.
Cope rails were often made for wrought iron railings and sometimes for cast iron railings. Railings mustn’t be welded to the cope rail. Lead or pins should be used instead.
Traditional fixing techniques such as pins, joints and screws are neat and have a low visual impact. Galvanised fixings shouldn’t be used as they speed up corrosion when in contact with iron.
Some iron founders have staff to install their products or you could use a reputable ironwork specialist or blacksmith with appropriate experience.
Find out about hiring a contractor.
Reinstating gates
Most cast iron gates were cast in one piece, although some are assembled from several components. Cast iron gates for domestic use were usually hung on ‘pintles’ (fixings) secured to a wall or gatepost. Pintles are often found still intact in masonry, even though the gate itself has been removed.
Making a pattern for a cast iron gate can be expensive. It’s worth checking first if the foundry has an appropriate pattern in stock.
- Previous
-
Painting
- Next
-
Permissions for work
Permissions for work
Permissions for work
You should check whether you must first apply for planning permission or any other type of consent before making any changes to historic ironwork. For listed properties, listed building consent may be required before repairs are made. Contact your planning authority to find out more.
Reinstatement
You may need to get permission to reinstate railings and/or gates before work begins on site. You should check with your planning authority. Listed building consent will be required if your property is listed.
Painting
If ironwork is listed or of special historical interest, the removal of original paint layers will need careful consideration and may merit the analysis of existing paint to work out the original colour scheme used.
Learn more about listed building and conservation area consent.
- Previous
-
Reinstatement
- Next
-
History
History
History
Cast and wrought iron were popular building materials during the late 1700s and throughout the 1800s. Mass production meant that much of the architecture of this period used iron both decoratively and structurally. Combinations of cast and wrought iron are not unusual.
Retaining traditional ironwork such as gates and railings can be hugely beneficial to the quality and character of a traditional building. Such period features add to the look and value of a property, and reinstatement of railings and gates is costly if they have been removed.
Iron was used for a wide range of architectural purposes including:
- structural columns and beams
- railings
- gates
- balconies
- finials
- ridge cresting
It’s often possible to identify the original makers and foundries by the marks they made on their cast iron products.
Loss of ironwork
Many buildings in Scotland have lost their original boundary ironwork (gates and railings) through damage or deterioration.
Much ironwork was given up for the war effort during the Second World War, and often little survives other than railing stubs in boundary walls. Original examples of ironwork were sometimes left in streets for future reference or where removal may have caused a safety hazard.
Ironwork production
Technological advances in the 1700s and 1800s enabled the mass production of wrought and cast iron, and iron production became a significant industry in Scotland.
Cast iron was used for much boundary ironwork from the 1820s onwards, as Scotland developed into a global centre for such work. Major architectural iron founders were set up across the central belt, and most towns had a foundry that might make simple railings.
Original castings were made from stock wooden patterns in grey iron, moulded in sand by hand. Wrought iron was manufactured from cast iron through the puddling process (heating and hammering by hand).
Wrought iron hasn’t been made since the 1960s, although it’s possible to source recycled wrought iron. The term ‘wrought iron’ is often mistakenly used to describe any kind of ornamental work in mild steel. ‘Wrought steel’ would be a more accurate description.
Contemporary work
There is much good contemporary work in mild steel, but this is often inappropriate for conservation or restoration purposes. Mild steel is also liable to corrode to a greater degree than either wrought or cast iron.
There has also been much ‘replica’ ironwork reinstated to imitate cast iron railing spears in particular. Most utilise steel bars and cast steel, or cast iron heads, welded together. Much of this work is poorly executed, employing modern fabrication techniques and modern materials with inappropriate designs.
Whilst it may be cheaper than using traditional materials and techniques, in the shorter term the aesthetics and longevity of this type of installation do not compare to using cast iron.
- Previous
-
Permissions for work
- Next
-
Contacts
Contacts
Contacts
Get in touch if you have any questions. We will be happy to help.
- Technical Research Team
- 0131 668 8951
- technicalresearch@hes.scot
- Previous
-
History
- Next
-
Resources
Resources
Resources
Professional institutions
Publications
Inform guides
An introduction to conservation and maintenance of traditional buildings for complete beginners.
Maintenance of Iron Gates and Railings
Other resources
- Previous
-
Contacts
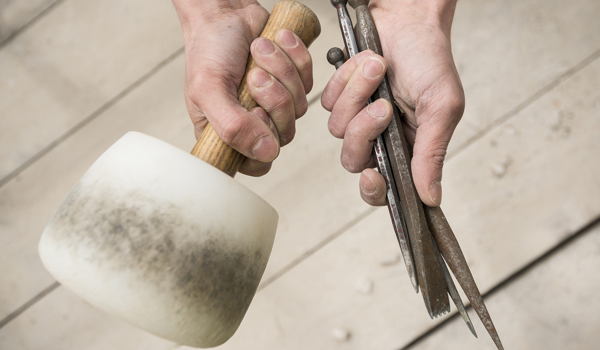
Hiring a contractor
Get advice on hiring a contractor including choosing a contractor and managing the work.